Bulk freight isn’t always easy to handle. When you’re collecting or delivering loose waste, woodchip, or agricultural produce, the job often needs a specific trailer setup.
That’s where the walking floor comes in.
In this guide, we’ll explain how walking floor trailers work, where they’re used, and what your fleet needs to operate them safely and legally.
We’ll also cover trailer types, health and safety, and sector opportunities—particularly for bulk and waste haulage work across the UK and EU.
What we’ll cover
What is a walking floor and how does it work?
A walking floor is a hydraulically powered trailer floor made up of slats that move in a sequence. It’s designed to gradually push material out the back of the trailer without tipping.
This unloading method keeps the vehicle stable at all times. That’s especially useful on uneven ground, at low-roof depots, or when working in built-up areas.

How a walking floor trailer unloads
The trailer’s bed is split into three sets of slats. These slats work together in a cycle:
- All three sets move backwards together, sliding the load towards the rear.
- Then, two sets hold firm while one returns to the front.
- This continues until the trailer is empty.
The process is smooth and controlled. Drivers can pause or reverse the movement, making it ideal for bulk sites with strict access limits or uneven terrain.
Benefits for haulage businesses
Using a walking floor trailer means you won’t need to lift or tip the trailer to unload. That reduces risks to the driver and others on site.
It also makes the trailer more flexible. You can unload in low-clearance areas, back into bays, or even on slopes.
Plus, walking floors aren’t just for loose material. Some haulage fleets use them for palletised goods on the return leg, adding more options for balancing outbound and inbound loads.
Trailer types for bulk material and waste transport
Not every trailer is built for loose, heavy loads. If you’re looking to expand your freight transport work in this space, it helps to know your options.
- Walking floor lorry: Often used for waste or recycling, it’s a rigid truck with a moving floor built into the chassis.
- Moving floor trailers: These are larger, articulated trailers with higher capacity. Good for biomass, bulk waste, or agricultural use.
- Tippers and ejectors: Still common, especially for construction loads, but less stable on uneven ground.
- Bulk tankers: Used for powders or liquids, not interchangeable with walking floors.
Adding one of these to your fleet could open new haulage and logistics contracts in the recycling, food processing, and energy sectors.
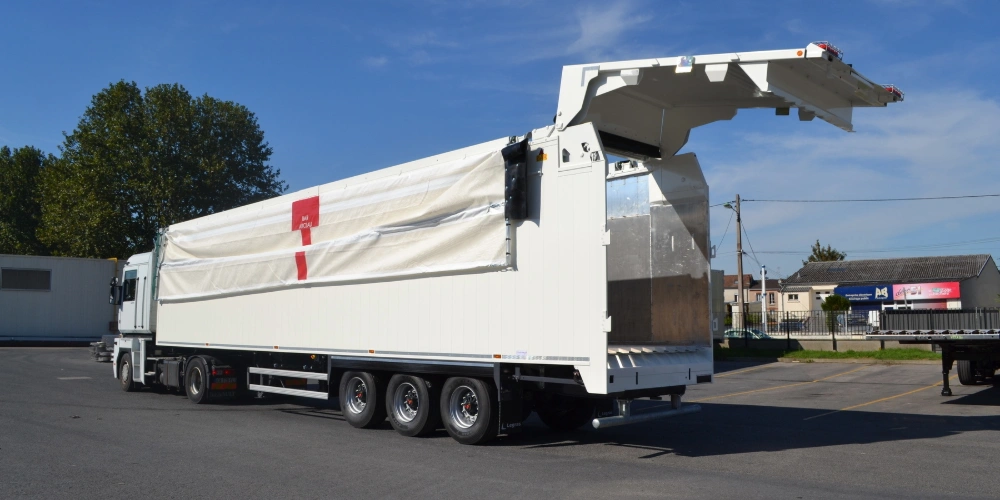
Where walking floors are used in haulage
The walking floor trailer is a staple in several sectors that deal with bulk materials. These industries often post regular work on load boards or book through freight forwarders.
- Waste and recycling: Household waste, commercial skip contents, and non-hazardous industrial material.
- Agriculture: Grain, fertiliser, animal feed, and silage.
- Woodchip and biomass: Often moved for energy production or industrial use.
- Retail backhauls: Some operators carry pallets or cages on the return leg, making better use of trailer space.
Companies and contracts to target
Local councils, waste management firms, and energy producers often use walking floor lorries. Many of these companies operate through brokered contracts, with some compliance expectations such as FORS accreditation.
Private-sector clients include food processors, sawmills, and manufacturers who need regular waste clearance.
These are typically high-volume contracts. Once you’ve proved reliability, they tend to bring long-term opportunities.
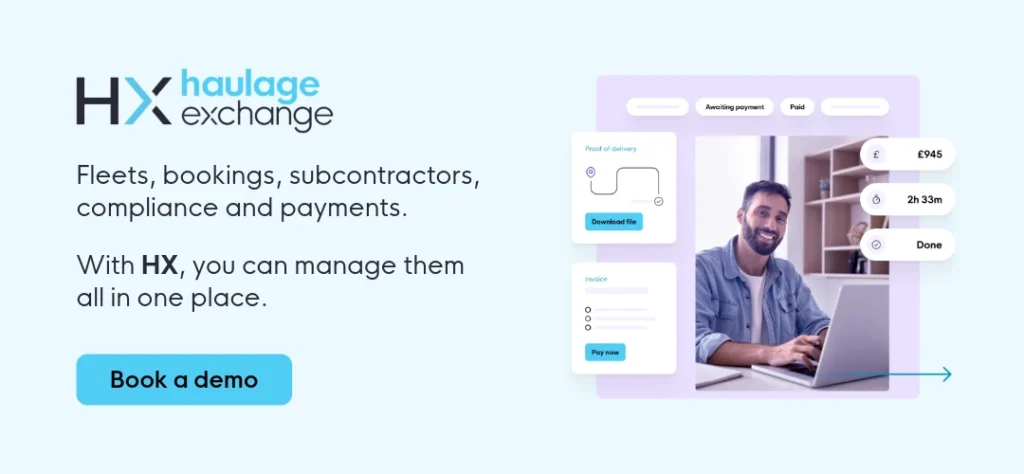
Health and safety considerations
Bulk material handling comes with its own risks, especially around unloading and site access.
- Load shift: Material can shift during transit if not packed evenly. A good driver risk assessment helps prevent rollover or instability.
- Site hazards: Uneven ground, narrow bays, or weather exposure can affect unloading. The floor’s non-tipping design helps reduce these issues.
- Contamination: Mixed waste or organic material may require the trailer to be cleaned between loads to prevent cross-contamination.
Driver training is especially important. Some firms include HGV driver training specific to walking floor operations, which helps avoid avoidable delays or load damage.
Compliance for bulk and waste loads
Whether you’re running across the UK or cross-border into the EU, compliance matters in bulk haulage.
Most walking floor loads fall under waste or agricultural rules, so you’ll need to stay up to date.
UK waste carrier and vehicle rules
If you carry waste, even non-hazardous material, you need a waste carrier licence from the Environment Agency. Loads also need to be accompanied by a waste transfer note showing what’s being moved and where.
Check your HGV operator licence to make sure your fleet is authorised for waste work. Some traffic areas may inspect operators more closely depending on the materials carried.
You’ll also need to keep vehicle condition in check. Walk-throughs or audits may focus on contamination control and the state of the unloading system.
EU transport and trailer compliance
When operating abroad, different rules may apply depending on the type of load and country. For example:
- Waste classification and labelling differ between EU nations.
- Loading and unloading protocols must follow EN standards in most regions.
- Some countries require special permits or licences.
For certain categories, like medical or chemical waste, ADR haulage rules apply. These don’t always affect walking floor work, but it’s worth checking if you transport hazardous loads.
Is a walking floor setup right for your fleet?
Before adding a walking floor trailer, think about your current contracts and the types of loads you’re equipped to handle.
Ask yourself:
- Are you regularly turning down bulk jobs due to lack of capacity?
- Do you have access to loading bays or sites with low clearance?
- Are there seasonal demand peaks in your area that could justify a specialised trailer?
- Would a non-tipping option reduce driver or site risk?
It’s also worth considering your current trailer mix. A flexible setup that allows for both loose and palletised goods could make your asset more useful year-round.
FAQs about walking floor haulage
What’s the difference between a walking floor trailer and a tipper?
A tipper unloads by lifting its bed at an angle, using gravity to slide the load out. A walking floor trailer uses a hydraulic system that moves the load without lifting. This keeps the vehicle stable and allows for unloading in tighter or uneven spaces.
Is a walking floor lorry better for mixed load types?
It can be, depending on the setup. Some operators use walking floor lorries for both bulk and palletised goods. That flexibility helps with return legs, especially if you’re running back from an area with fewer bulk opportunities.
How much can you carry in a moving floor trailer?
Most UK-spec moving floor trailers can carry up to 90–100 cubic metres of loose material, depending on the material density and legal payload.
Double-check your trailer’s unladen weight against UK lorry dimensions and axle limits before loading.
Do I need a special licence to operate walking floor trailers?
No separate driving licence is required, but you do need to be trained in the hydraulic floor system. Many companies now include this in their standard HGV driver training. If you’re handling waste or hazardous loads, you may also need a waste carrier licence or ADR haulage certification.
What sectors regularly use walking floor haulage?
The most common sectors are waste and recycling, agriculture, biomass, and retail. Contracts often come from councils, brokers, or processing plants. It’s a strong option for growing your presence in freight transport, especially where tipping trailers aren’t practical.