DVSA roadside inspections are a core part of maintaining road safety and compliance in the haulage industry.
A well-prepared fleet not only avoids fines and delays but also helps maintain a professional reputation. For haulage companies, staying inspection-ready is an important part of running a safe, compliant operation.
In this guide, we’ll cover the essentials of DVSA roadside checks, from vehicle inspections to driver risk assessments, and tips on maintaining DVSA fleet compliance.
Understanding DVSA roadside inspections
DVSA roadside inspections are unannounced checks conducted by the Driver and Vehicle Standards Agency to assess the safety and compliance of commercial vehicles and their drivers.
These inspections aim to ensure that all vehicles on the road meet legal standards for roadworthiness, driver records, and overall compliance with DVSA regulations.
Inspections cover various aspects, including vehicle condition, driver documentation, and operating licences, to verify that commercial vehicles are both safe and legally compliant.
Failing a roadside inspection can lead to fines, penalties, and operating restrictions, and may result in vehicle impoundment. These consequences can directly impact fleet productivity and damage the company’s reputation, making regular preparation for these checks essential.
Key areas inspectors focus on during DVSA fleet inspections
During a roadside inspection, DVSA inspectors evaluate several areas to assess vehicle safety and compliance.
Here are the primary items they review:
- Vehicle roadworthiness: Inspectors check the vehicle’s condition, focusing on brakes, tyres, lights, and steering systems.
- Driver hours and tachographs: Inspectors verify compliance with tachograph rules, ensuring driver hours stay within legal limits and records are accurate.
- Load security: Loads must be secured correctly to avoid shifting or accidents on the road. Inspectors verify that load restraints are effective.
- Vehicle documentation: Inspectors check for proper vehicle and operator licences, MOT certificates, haulage insurance and other necessary documents.
- Driver qualifications: The driver’s licence, CPC (Certificate of Professional Competence), and any additional certifications are reviewed.
- Exhaust emissions: Vehicles must meet emissions standards, with inspections ensuring that no tampering or bypassing of emission controls has occurred.
- Maintenance records: Inspectors review maintenance records, ensuring vehicles have undergone regular checks and necessary repairs.
For a full list of what’s covered in DVSA roadside inspections, please refer to the DVSA’s official guide here.
Fines and restrictions for non-compliance
Non-compliance with DVSA roadside inspection standards can lead to several consequences:
- Fines: Drivers and fleet operators may receive fines for each violation. Fines vary depending on the issue’s severity, with penalties applied to drivers, operators, or both.
- Prohibition Notices: A prohibition notice may be issued if a vehicle is deemed unfit to be on the road. This notice requires the vehicle to be taken off the road until all issues are resolved.
- Points on operator licences: Violations can add points to an operator’s licence, potentially leading to its suspension if limits are exceeded.
- Impoundment: In severe cases, vehicles may be impounded, which disrupts operations and leads to costly recovery processes.
It’s essential for fleet managers to stay on top of DVSA requirements to avoid these penalties, maintain a strong compliance record, and protect their operational licences.
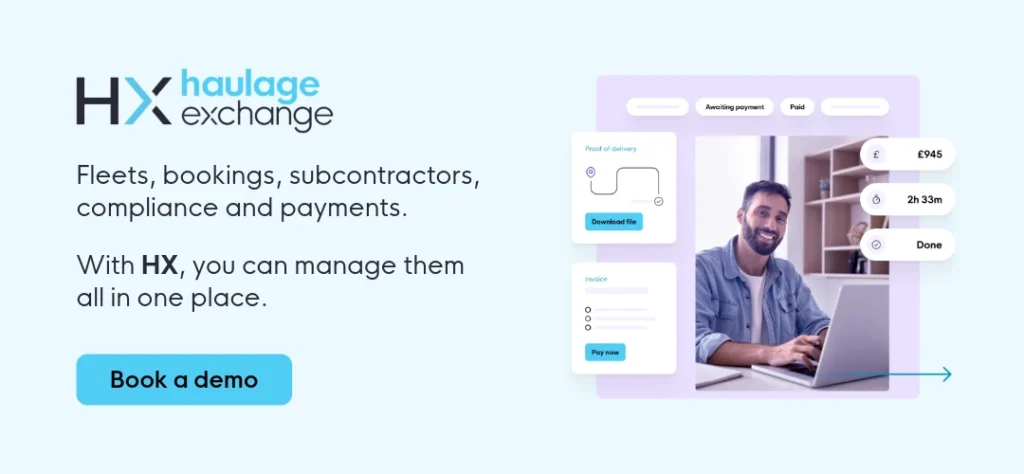
Conducting driver risk assessments
Driver risk assessments are an important step in ensuring both driver safety and DVSA fleet compliance, as they help you identify potential risks, support drivers, and maintain a professional standard.
Assessing driver qualifications and training
Regularly verifying driver qualifications and training ensures that all drivers meet compliance standards. Confirm that your drivers hold up-to-date HGV licences and have undergone HGV driver training. Continuous training not only maintains safety standards but also prepares drivers for roadside inspections.
Monitoring driver hours and tachograph use
Monitoring driver hours reduces the risk of fatigue-related accidents and helps meet DVSA requirements.
By using tachographs and driver records, fleet managers can track hours to prevent violations. This is where TMS integrations can play a role, helping to monitor driver schedules, reduce fatigue, and improve driver performance.
Ensuring vehicle compliance and roadworthiness
Maintaining a well-prepared fleet is central to passing DVSA roadside inspections. Regular vehicle checks and detailed maintenance records help keep your haulage vehicles compliant and ready.
Routine vehicle maintenance checks
A proactive maintenance schedule can keep your vehicles safe and reliable.
Routine checks should cover key components, such as brakes, tyres, lights, and steering. When vehicles are maintained on a regular basis, you minimise breakdown risks and are prepared for inspection at any time.
Documenting vehicle maintenance and repairs
Keeping a comprehensive record of vehicle maintenance and repairs shows a clear history of safety checks and repairs.
This documentation demonstrates your commitment to DVSA fleet compliance and can be valuable during inspections. Maintenance logs should cover all checks, repairs, and parts replacements, allowing you to show proof of compliance and your commitment to safety.
Preparing for on-the-spot checks
DVSA roadside inspections are unannounced, so preparing your drivers for on-the-spot checks is essential.
A good example of this is the below video from YouTuber Pete the Courier, who recently experienced a DVSA roadside inspection for himself – he was mostly compliant, but made a few honest mistakes on his tachograph.
Training your drivers on handling inspections and keeping necessary documents on hand ensures a smoother process.
What drivers should know about DVSA roadside inspections
Drivers should understand the inspection process and know what documents they need to provide.
Training drivers on inspection etiquette and compliance requirements ensures they can handle the process professionally. Key documents include tachograph records, driving licences, and the operator’s fleet management records.
Common issues flagged in DVSA roadside inspections
Certain issues frequently cause non-compliance, such as missing documents or overdue maintenance.
Common violations include incomplete driver records, overdue vehicle inspections, and improper load security. Conduct regular checks to spot these issues early and maintain high inspection pass rates.
Creating a DVSA compliance culture within your fleet
Establishing a compliance-focused culture in your fleet helps reinforce safety standards and reduces the risk of penalties.
By encouraging a proactive approach, you build a team that’s fully prepared for inspections.
Regular training and updates for staff
Regular training keeps drivers informed on DVSA regulations and inspection processes.
Offering refresher courses on managing haulage drivers and ensuring compliance with safety standards helps embed these practices into daily operations. Updating drivers on any changes to DVSA requirements maintains compliance and builds confidence for inspections.
Benefits of prioritising DVSA fleet compliance
Investing in DVSA fleet compliance brings lasting benefits. Staying compliant helps you avoid costly fines, maintain safety, and improve customer trust. A strong compliance record also boosts your fleet’s reputation, opening doors to new contracts and long-term partnerships.
Conclusion
Preparing your fleet for DVSA roadside inspections involves regular maintenance, driver training, and thorough record-keeping.
By proactively managing these aspects, haulage companies can maintain DVSA fleet compliance, reduce risk, and improve fleet performance.
A commitment to compliance not only keeps your fleet on the road but also supports a safe and reliable business model.